In the age of Covid-19, the need for industries to adopt advanced technologies, incorporate more health and safety standards into their daily operations, and maintain a robust workforce is more important than ever.
The Agricultural Technology Research Program (ATRP) at the Georgia Tech Research Institute (GTRI) is leading efforts to equip Georgia's agribusiness and food processing industries with the technology and skills to remain competitive and at the forefront of the global transformation that has been accelerated by the pandemic. ATRP works in collaboration with university and industry partners, especially within Georgia's poultry industry – which has a $28 billion annual impact on the Georgia economy – on projects involving robotics, advanced sensors, environmental treatment, and worker and food safety technologies. ATRP's ultimate goal is to transition technologies from concept to commercialization as quickly and economically as possible.
"Our role is to support the agriculture industry in the state of Georgia and the world – we are Georgia-focused first, but what we do in Georgia is going to impact the world," said Doug Britton, a GTRI principal research engineer and ATRP program manager.
Video: GTRI ATRP Overview
Problem Solved
The ATRP's origins date back to 1973, when the Georgia Poultry Federation requested engineering support from GTRI and Georgia Tech on issues troubling the poultry industry. The Georgia Poultry Federation represents the Georgia poultry industry's interests at the state and federal levels on legislative and regulatory issues.
"They received concerns from neighbors and friends about all of the noise coming out of mills used to make animal feeds," Britton said. "So, they asked Georgia Tech to do acoustics analysis to see if there was some way to reduce those noise levels."
From there, ATRP was born.
ATRP conducts state-sponsored and contract research for industry and government agencies. For FY 21, ATRP received roughly $2 million in funding from the state of Georgia. ATRP's Automation and Robotics Research received the majority of that funding, at 41%, followed by Technology Transfer/Outreach/Technical Assistance, which received 16%. Environmental and Biological Systems Research came in third at 14%; followed by Food Safety Research at 13%; Program Support with 9%; and Imaging and Sensor Research at 7%.
ATRP benefits from significant industry support, with 15 companies and associations actively participating in research projects. In addition, over 35 individuals sit on the ATRP industry advisory committee, representing 28 different companies and organizations. For FY 2021, ATRP had nine research prototypes in various stages of development; five exploratory research projects; three provisional patent applications; five invention disclosures; 33 published articles, papers, and presentations; 18 participating industry and academic partners; and 21 technical assistance service requests fulfilled.
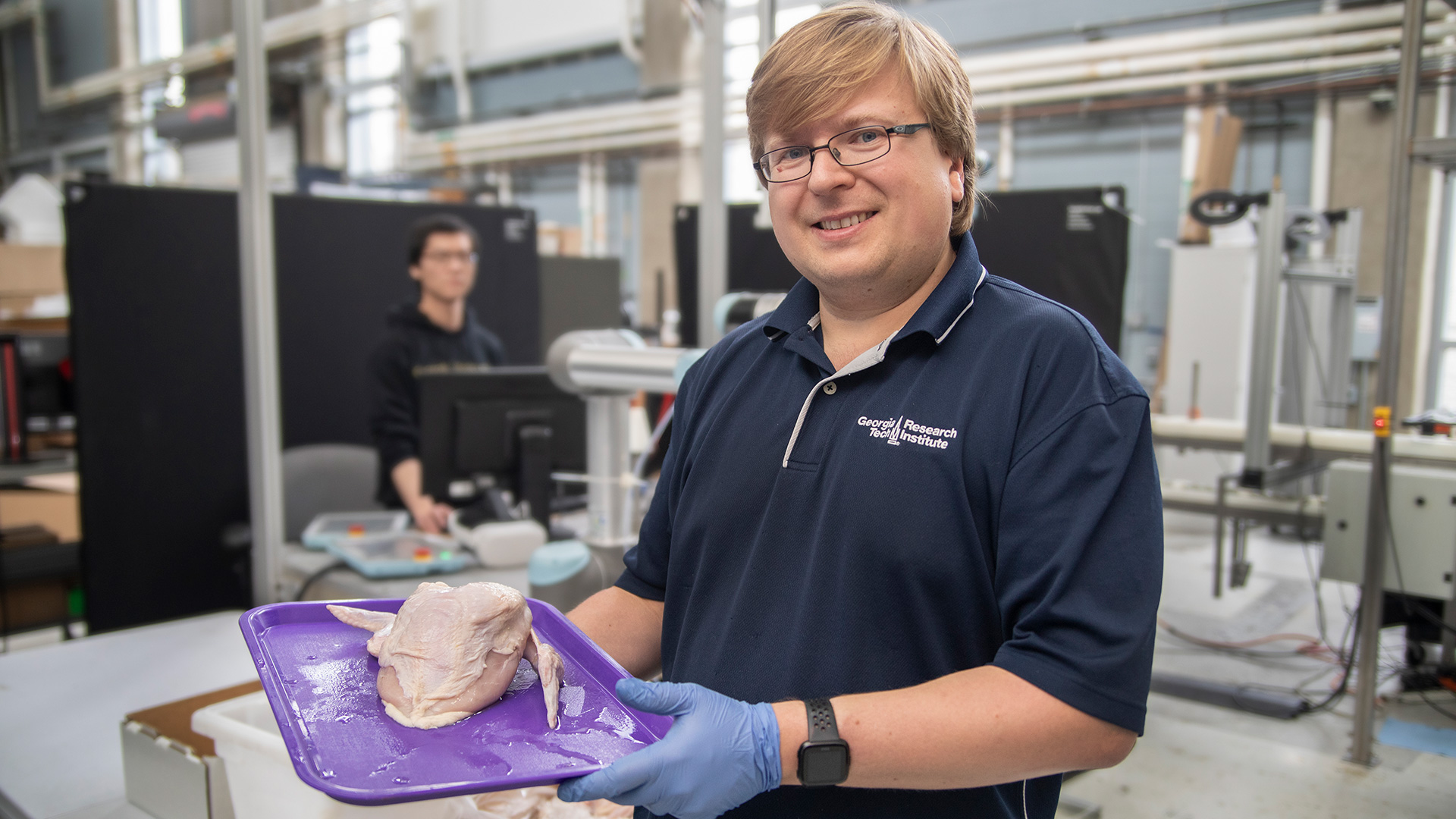
GTRI Research Engineer Konrad Ahlin (pictured) said applying VR to common poultry processing operations, such as cone loading, could usher in a new era of how humans and robotic devices work together to accomplish tasks (Credit: Christopher Moore, GTRI).
VR to the Rescue
One of ATRP's provisional patents relates to its work around incorporating automation solutions, specifically virtual reality (VR), into poultry processing to boost efficiency and enhance worker safety.
Working in a poultry processing plant can be challenging.
Food processing environments are often kept quite cold by design to prevent pathogen growth. Low temperatures, combined with the physical demands of the job, have contributed to the industry’s high turnover rates that have been exacerbated by the pandemic. According to recent estimates, annual poultry worker turnover can be as high as 100%, and amid Covid-19, increased risks for disease transmission and cross-contamination pose even more obstacles for the sector.
To address these issues, ATRP is exploring ways to combine VR with factory-based robotics in certain poultry processing operations, such as cone loading, which could allow workers to perform their jobs in safer environments – or even from home. Cone loading is when chicken carcasses that have had their legs and thighs removed are placed onto a cone for further processing.
"Cone loading sounds like a really easy task, and it is," said Konrad Ahlin, a GTRI research engineer who has expertise in robotics. "But the problem is having a dedicated person doing that for extended periods – it's physically demanding on the person, and it's a menial, trivial task that's unfortunately just necessary."
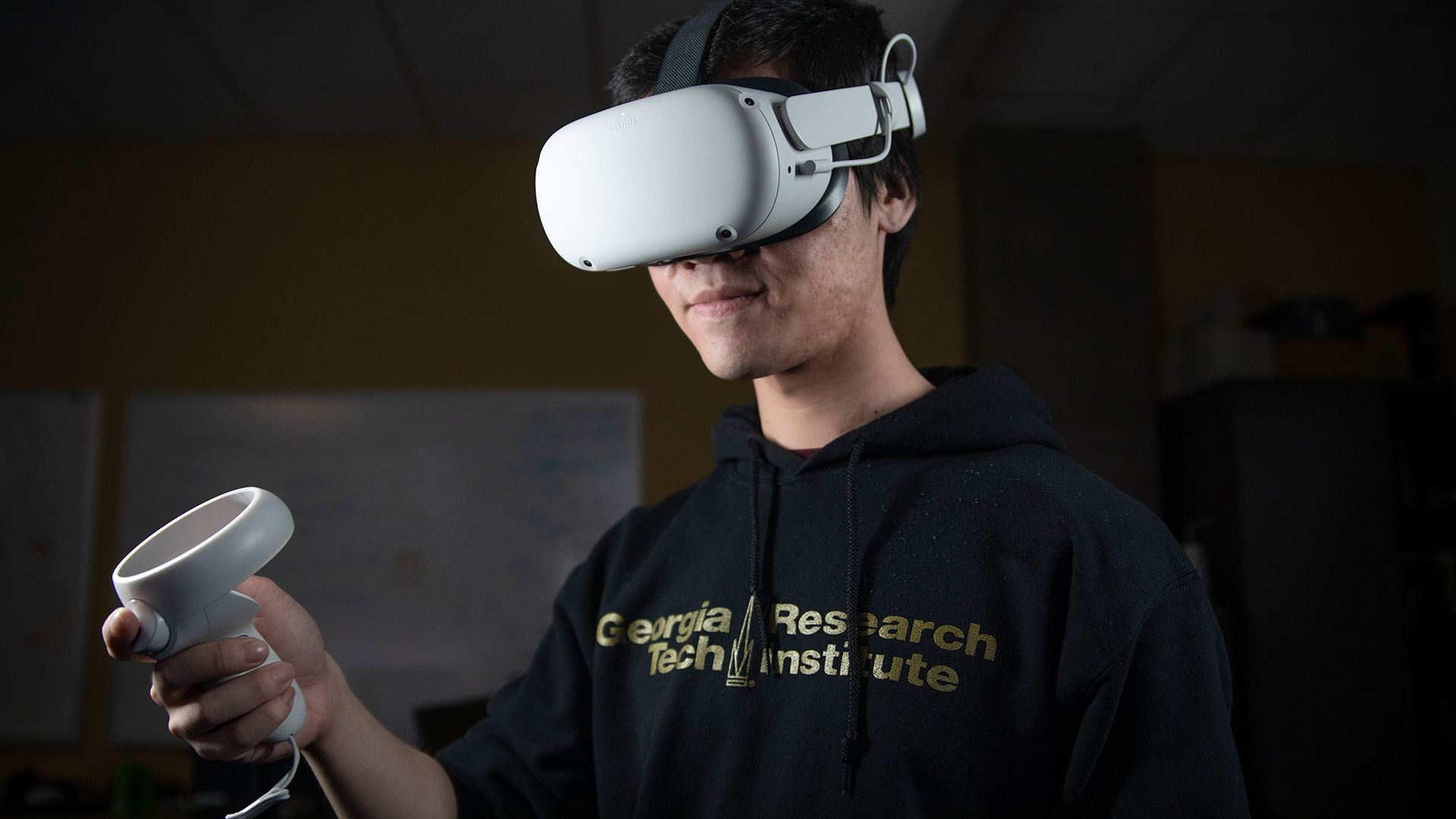
ATRP's efforts to incorporate VR technology into poultry processing could allow some human workers to perform their jobs from anywhere in the world (Credit: Christopher Moore, GTRI).
ATRP's "expert-in-the-loop" robotics solution would allow human workers to provide key information to robot systems performing the operation – all from a virtual reality environment. So far, attempts to fully automate common poultry processing operations have not been successful due to chickens' irregular and malleable shapes. But VR could solve that challenge, Ahlin noted.
"Virtual reality is creating this bridge where information can intuitively pass between human operators and robotic devices in a way that hasn't been possible before," Ahlin said.
ATRP has filed a provisional patent for its VR research and is also working with the Georgia Research Alliance (GRA) to develop a commercialization roadmap for the technology. The GRA is an Atlanta-based nonprofit that expands research capacity at Georgia universities, then seeds and shapes startup companies around inventions and discoveries.
Gary McMurray, a GTRI principal research engineer and division chief of GTRI's Intelligent Sustainable Technologies Division, said VR's potential to defy geographic limitations could be transformative for the manufacturing industry at large.
"There are lots of reasons that this technology could have a big impact on manufacturing, which is struggling with finding people to do jobs," McMurray said. "With this technology, you could be sitting in West Virginia, put on a VR headset, and work from the comfort of your home. You're no longer tied to geography, and that's really powerful."
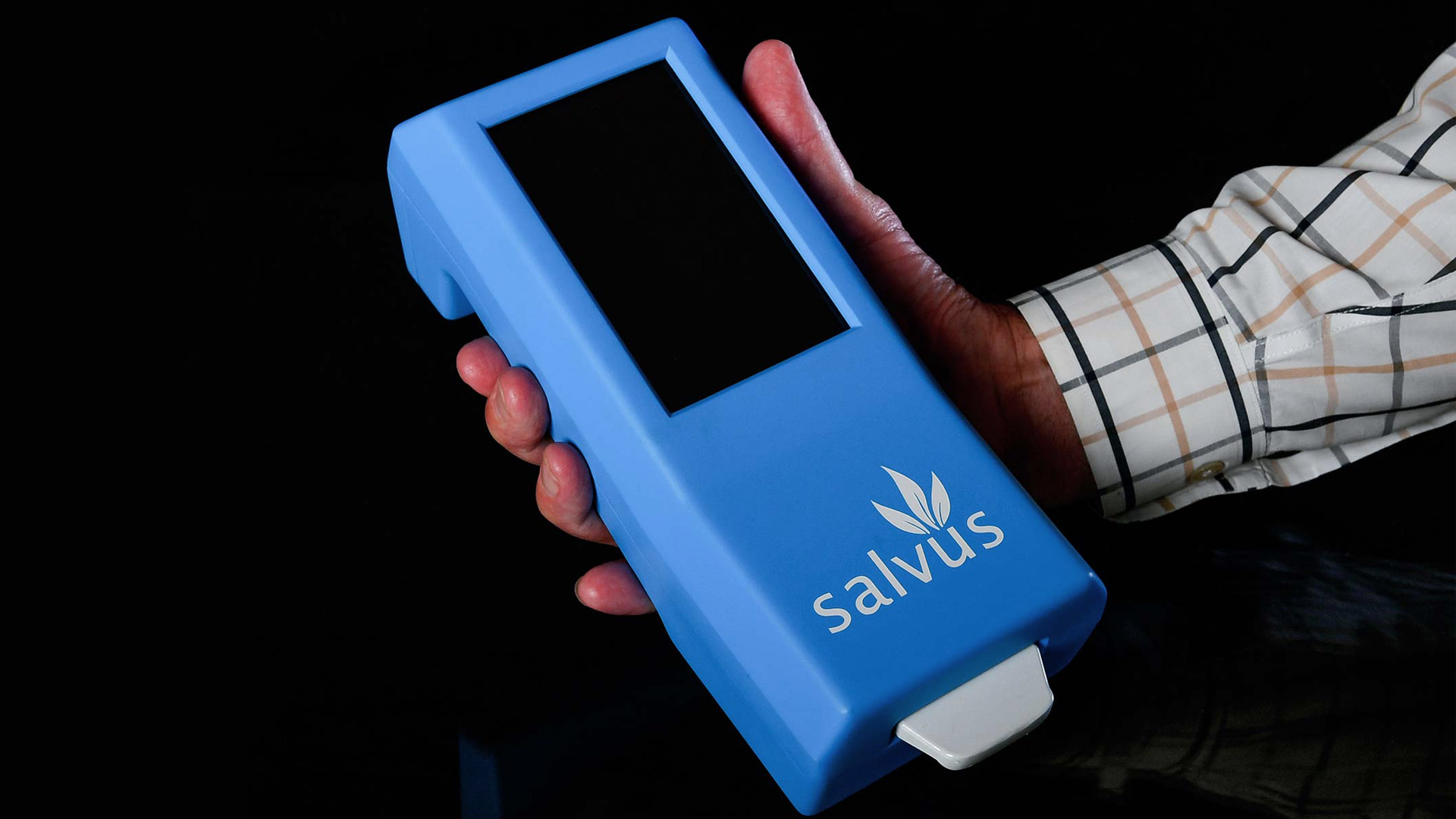
ATRP's interferometric biosensor has been licensed exclusively to Valdosta, Ga.-based Salvus™, which is a part of the CJB® family of companies. The technology can be configured to detect a variety of pathogens and chemicals across multiple industries in a matter of minutes or seconds (Credit: Salvus).
Concept to Commercialization
Many ATRP projects are already having an impact outside the lab.
Interferometric Biosensing
One of those is an interferometric biosensor that can be configured to rapidly detect a variety of pathogens and chemicals across multiple industries. The technology has been licensed exclusively to Valdosta, Ga.-based Salvus™, which is a part of the CJB® family of companies.
Salvus, which develops and manufactures chemical contaminant and pathogen detection technologies for the food and agriculture, life sciences, water quality, and specialty chemical industries, has said it expects to begin clinical and market trials for the biosensor sometime in 2022.
“We have been able to apply our commercialization and manufacturing experience to the breakthrough work that Dr. Xu and the ATRP team have accomplished," said Ron Levin, director of strategy for Salvus. "It is rewarding to discuss this technology with potential commercial partners and to hear their excitement for the technology in so many potential applications.”
Jie Xu, a GTRI principal research scientist who is leading the Salvus project, said her team is currently working with Salvus to ensure the technology's core electrical, mechanical, and chemical functions perform seamlessly ahead of deployment.
"In a controlled environment, such as a lab, the technology works beautifully," Xu said. "But when you move it outside of the lab, you have to account for a lot of unknown factors."
The science behind the Salvus detection system is called interferometry, which exploits the interference of light waves to precisely determine the rate at which target particles attach to the sensor's surface. The sensor contains two separate channels – a sensing channel and a reference channel.
The sensing channel detects the specific target of interest, such as a virus or chemical. This signal is then compared to the reference channel, which allows the sensor to quantify the level or amount of the specific target and provide an accurate reading. A major benefit of the technology is its ability to complete tests in a matter of minutes or seconds. In a medical setting, a device utilizing this technology would allow clinicians to process a patient sample and have results ready before the patient leaves the premises – eliminating the need to send patients home to await lab testing results. Meanwhile, at a water processing facility, workers would be able to use this device to test the water and immediately know how much treatment is required.
The technology has been tested in more than 50 diverse applications, including the detection of Covid-19, Salmonella, avian influenza, and many different chemicals.
"Salvus came to us and asked if we could research ways to speed up in-the-field testing of pathogens and chemical contaminants," Xu said. " So, instead of a company sending a sample to the lab and waiting weeks to get the lab results, our proprietary technology would produce results right on the spot."
Dynamic Filtration
Another project making headway in the commercial space is ATRP's Dynamic Filtration System. ATRP conducted in-plant trials of the patented filtration technology in FY 2021. During the trials, the system was licensed for poultry processing by Watson Agriculture and Food, a subsidiary of venture capital firm Watson Holdings that invests in technologies to solve major world problems.
The technology consists of a unique filtration system that is designed to separate various levels of solids, fats, and other materials from wastewater used in poultry processing. The process keeps the filtered materials from clogging the system, allowing for greater throughput. In addition, it captures the filtered materials that have additional value as a byproduct. Current work is focused on screening smaller particles to further improve water recyclability and wastewater treatment in poultry processing.
"Universities are excellent at finding problems to solve, and I chose to partner with Georgia Tech for its reputation as being a leading research institute that has some of the best engineers in the world," said Trey Watson, founder and CEO of Watson Holdings. "Even though water filtration is just one component of the poultry production process, it greatly enhances consumer safety and is both cost- and energy-efficient for the poultry industry, and I am excited to continue working with Georgia Tech and GTRI as we create additional solutions for tomorrow's problems."
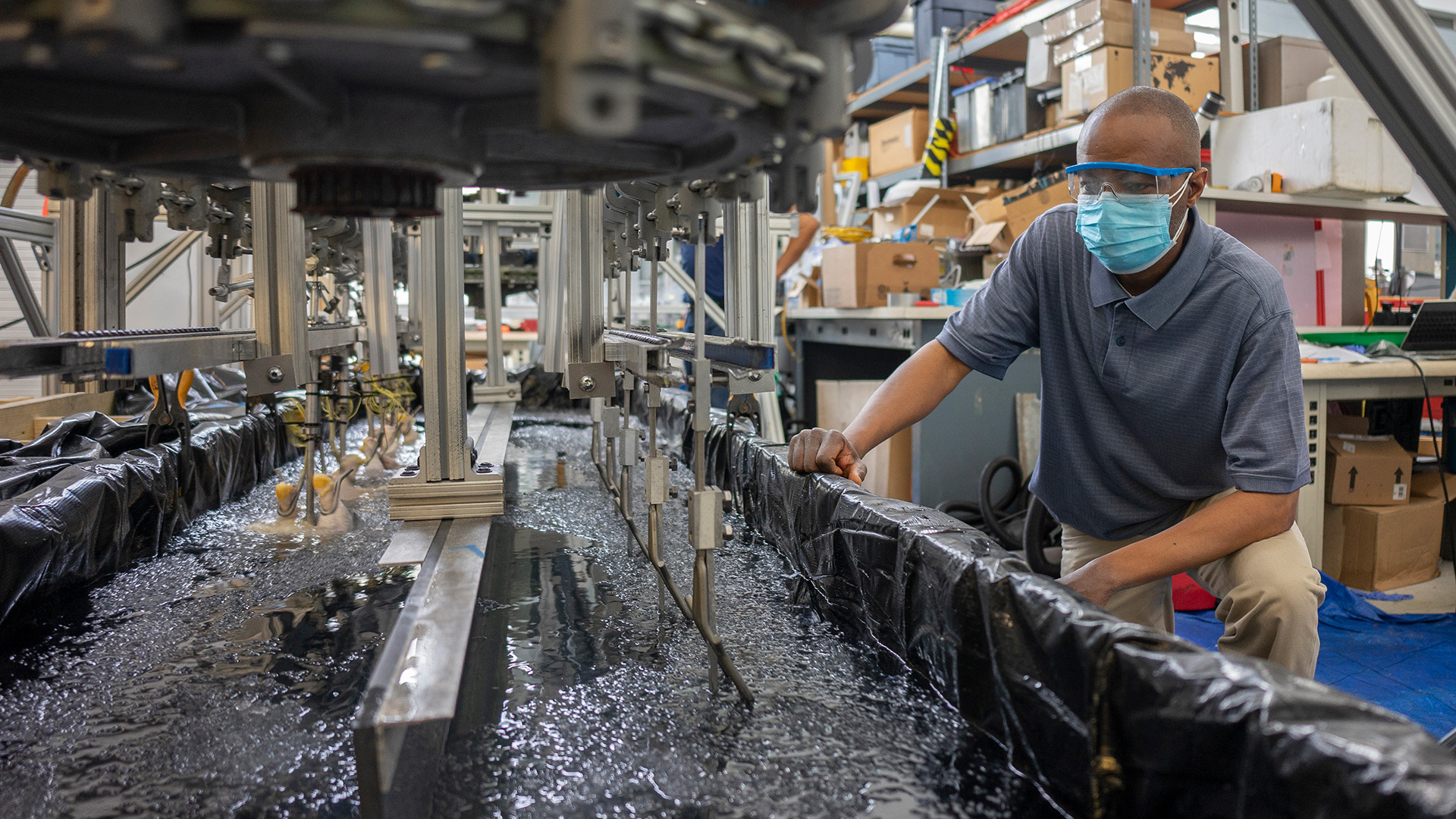
Comas Haynes (pictured) is a GTRI principal research engineer and principal investigator (PI) for ATRP's rotational poultry chilling research. Haynes said ice slurry is beneficial compared to conventional liquid water when chilling chicken carcasses because it can be pumped like a liquid, and its liquid nature allows it to really go around the contour of the carcasses to result in faster chilling times (Credit: Christopher Moore, GTRI).
Ice in Motion
Nearly everyone remembers the Slurpee slushies found at their local 7-Elevens.
ATRP researchers are applying a similar concept, along with rotational kinematics, to poultry processing to ensure product quality and safety. A distinction between ATRP's ice slurry mixture and Slurpee slushies is that the ice particles ATRP uses are finer, and its ice slurry blend is more homogenous.
During processing, chicken carcasses are typically immersed in screw augers of chilled water to lower their temperature to a degree that prevents pathogen growth. A screw auger is a mechanism used in bulk handling that utilizes a rotating helical screw blade to move liquid or granular materials through a shaft. However, this process requires carcasses to be removed from a shackle line before immersion, which can result in lost traceability; increased cross-contamination risks due to direct contact between carcasses; and additional labor to rehang the carcasses onto processing line shackles after chilling.
ATRP is working to solve these challenges by keeping carcasses shackled during the immersive chilling process. For the chilling medium, ATRP is using either conventional chilled water or ice slurry, which is a mix of tiny ice crystals and liquid water. Compared to conventional liquid water, ice slurry provides the additional chilling effects of ice while retaining a liquid-like form that is easily transportable and could result in higher cooling rates.
"One thing about ice slurry is that you can pump it like a liquid instead of trying to load it and carry it around like traditional ice," said Comas Haynes, a GTRI principal research engineer who is leading the project. "And because of its liquid nature, it can really go around the contour of the carcasses, which results in faster chilling times."
The team has built a new carousel-type test rig that better mimics real-world conditions, wherein the carcasses remain shackled during immersive chilling to alleviate the aforementioned screw conveyor issues. The addition of passive, or non-motorized, rotational effects along with conventional “line speed” translation is producing promising reductions in chill time. This has already been shown for chilled water, and there is a near-term plan to test this enhancement in ice slurry as well, Haynes said. Georgia Tech has also filed a patent on its rotational chilling enhancement research.
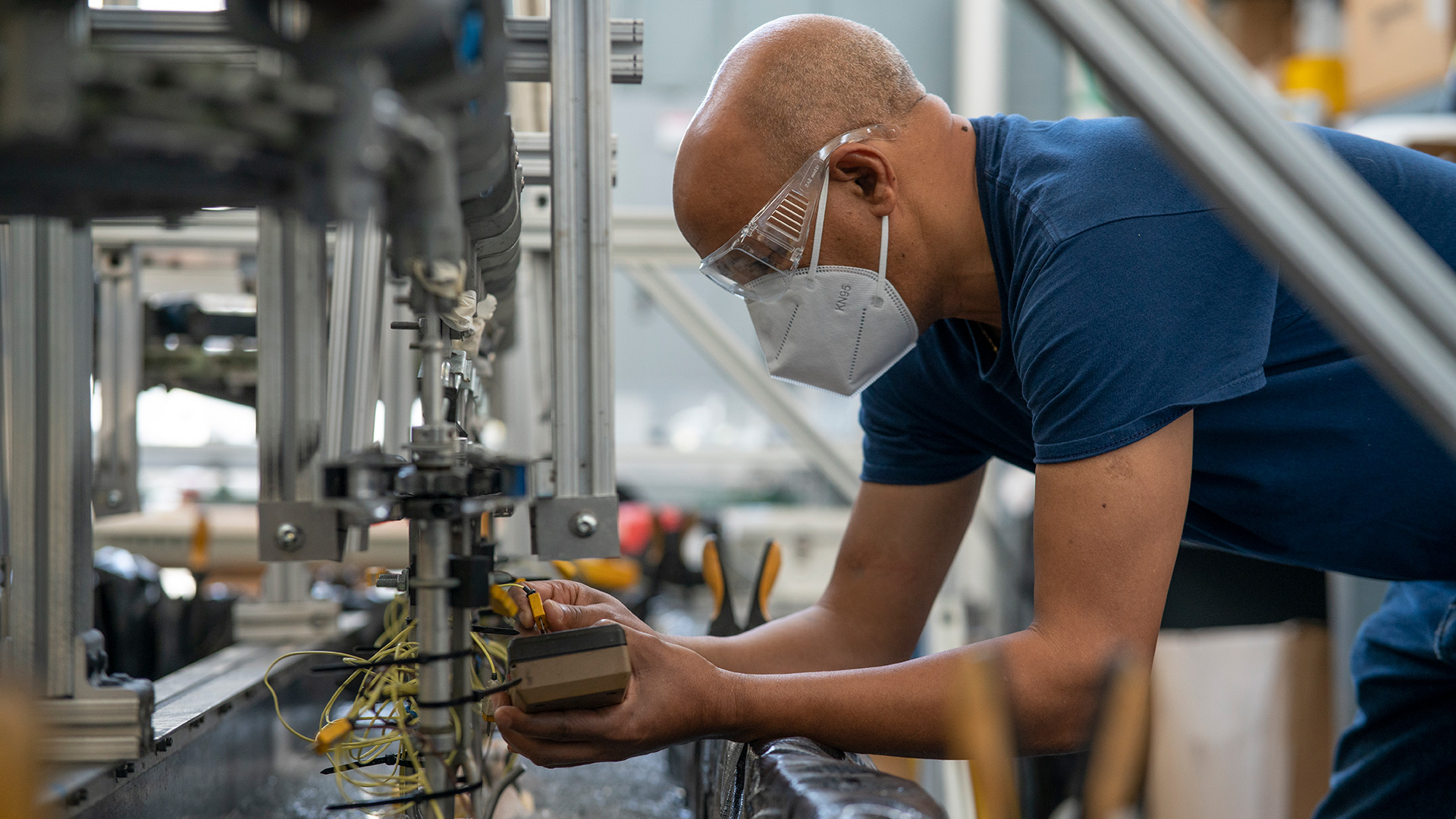
GTRI Principal Research Engineer Aklilu Giorges (pictured) conducts research on ATRP's rotational poultry chilling system (Credit: Christopher Moore, GTRI).
Failing Forward
Whatever the project, ATRP continuously seeks to translate novel research concepts into commercially viable products for poultry, agribusiness, and food manufacturing industries in Georgia, the nation, and the world, that maximize productivity and efficiency, advance safety and health, and minimize environmental impacts.
"We want to be viewed as thinking outside the box – that's part of our role, and we embrace it," Britton said. Britton added that GTRI provides industry partners with a safe environment to take risks and the cutting-edge technologies to achieve maximum success.
"I always tell my industry stakeholders that GTRI is a great place to fail," Britton said. "If we fail here, it means we don't fail out there."
Writer: Anna Akins (anna.akins@gtri.gatech.edu)
GTRI Communications
Georgia Tech Research Institute
Atlanta, Georgia USA
MORE 2022 ANNUAL REPORT STORIES
MORE GTRI NEWS STORIES
The Georgia Tech Research Institute (GTRI) is the nonprofit, applied research division of the Georgia Institute of Technology (Georgia Tech). Founded in 1934 as the Engineering Experiment Station, GTRI has grown to more than 2,800 employees supporting eight laboratories in over 20 locations around the country and performing more than $700 million of problem-solving research annually for government and industry. GTRI's renowned researchers combine science, engineering, economics, policy, and technical expertise to solve complex problems for the U.S. federal government, state, and industry.